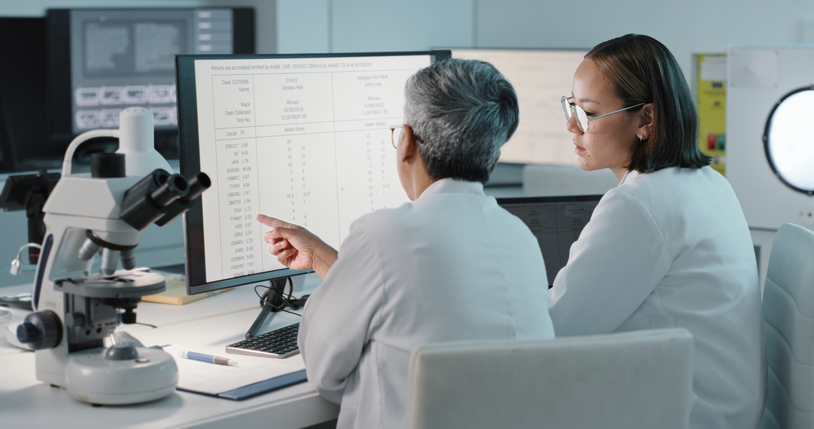

Credit score: Kobus Louw/Getty Photos
A biopharmaceutical business govt not too long ago shared a telling perception with one in every of my colleagues. He mentioned all his friends wish to “select the drapes within the penthouse of AI-powered drug improvement, however everybody forgot they should pour the muse and set up the plumbing first.”
His sentiment completely captures the problem going through biopharma as we speak. As firms race to implement synthetic intelligence throughout their operations, a big impediment threatens to derail these efforts: the scientific knowledge disaster. Nowhere is that this obstacle extra urgent than in Chemistry, Manufacturing, and Controls (CMC) writ giant.
CMC, the processes guaranteeing therapeutics will be safely and persistently manufactured at scale, characterize the bridge between promising lab discoveries and life-saving therapies for sufferers. But this important operate has grow to be a key space of impression for biopharma’s knowledge disaster, with wide-reaching implications for manufacturing effectivity, regulatory compliance, and in the end affected person entry to therapies.
Hidden manufacturing bottleneck
Whereas manufacturing innovation typically focuses on gear, facility design, and course of optimization, the underlying knowledge infrastructure connecting these components stays surprisingly antiquated. CMC scientists designing purification strategies, figuring out stability, and scaling up manufacturing are drowning in fragmented knowledge throughout tons of of proprietary techniques.
Novartis CEO Vas Narasimhan candidly acknowledged this problem when he famous in a podcast interview, “We’ve needed to spend more often than not simply cleansing the information units earlier than you’ll be able to even run the algorithm. It’s taken us years.” Our current analysis with CMC specialists from main firms, together with Amgen, Bayer, GSK, Novartis, and Takeda, revealed that scientists waste 25-100 hours weekly on handbook knowledge transcription between techniques. Immediately, expert professionals spend as much as 80% of their time wrestling with knowledge as an alternative of advancing science.
Why CMC knowledge is uniquely difficult
The manufacturing setting presents distinctive knowledge challenges that aren’t current in different areas of drug improvement. CMC knowledge should bridge medical improvement and industrial manufacturing, join analytical and course of knowledge, and preserve sturdy lineage for regulatory compliance.
Three components make CMC knowledge significantly troublesome to handle:
- Numerous instrumentation panorama: A typical manufacturing setting would possibly make the most of tons of of various instrument varieties from varied distributors, every producing knowledge in proprietary codecs.
- Regulatory documentation necessities: Manufacturing knowledge should preserve traceability and provenance for regulatory filings and investigations.
- Doc-centric workflows: Regardless of digitization efforts, most CMC processes stay document-centric fairly than data-centric, with data trapped in PDFs and textual content information fairly than structured databases.
The implications prolong past inefficiency. Vital connections between early predictive stability knowledge and precise outcomes grow to be not possible to make, hampering course of understanding. Predictable and preventable manufacturing deviations go undetected till they trigger batch failures. Tech switch between improvement and manufacturing websites turns into needlessly time-consuming and complicated.
Regulatory storm on the horizon
This knowledge fragmentation drawback will face further strain as regulatory companies transfer towards necessary digital CMC submissions by 2026. With no basic rethinking of information infrastructure, firms face the prospect of pricey, handbook knowledge aggregation workout routines for every submission. Our research discovered that 80% of CMC organizations recognized late-phase portfolio acceleration as their high enterprise problem. But this acceleration is not possible with out addressing the underlying knowledge basis.
Ahead-thinking firms are already addressing this problem by implementing purpose-built scientific knowledge platforms for manufacturing. These options ship concrete outcomes. One of many high 10 life sciences firms we labored with eradicated 25-100 hours weekly of handbook transcription of their purification course of improvement, saving $375,000 yearly in only one slice of their operation. Of their bioprocessing operations, one other biologics producer decreased time-to-insight from one week to at some point. A gene remedy developer elevated throughput 6X by automating qPCR knowledge workflows.
Probably the most profitable implementations share three traits:
- They prioritize knowledge replatforming: Shifting knowledge from proprietary codecs to open, standardized codecs within the cloud creates the muse for all different capabilities. For instance, as an alternative of getting knowledge locked in vendor-specific information from every instrument, the platform mechanically converts it to a constant format like JSON or Parquet. Harmonizing knowledge allows simpler evaluation and integration with different techniques.
- They implement knowledge context and lineage: Sustaining the relationships between samples, strategies, devices, and outcomes allows regulatory compliance and scientific insights. A contemporary knowledge platform tracks each step within the course of, from the uncooked supplies to the ultimate product, recording who did what, when, and with what gear. Such a platform offers immutable audit trails for regulatory functions and permits scientists to grasp how course of parameters have an effect on product high quality.
- They concentrate on scientific use instances: Not like generic knowledge options, profitable scientific knowledge platforms construct upon particular manufacturing workflows like bioprocess improvement, formulation, and product high quality and stability testing. As a substitute of a general-purpose database, the platform offers instruments tailor-made to the wants of every workflow, similar to methodology efficiency trending in chromatography or real-time monitoring of bioreactor parameters.
Past effectivity–constructing scientific intelligence
The true potential of recent knowledge infrastructure goes past effectivity beneficial properties. You get a brand new scientific intelligence when knowledge flows seamlessly from course of and analytical devices right into a unified platform.
High quality groups can predict stability outcomes primarily based on manufacturing situations as a result of the platform offers a unified view of course of and analytical knowledge, enabling development evaluation and modeling. Engineers can establish course of parameters influencing product high quality by multivariate evaluation because of the platform’s potential to combine knowledge from varied sources and supply superior analytics instruments. Groups involved with product lifecycle administration could make knowledgeable choices utilizing historic manufacturing knowledge from related merchandise. The platform creates a centralized information base of producing knowledge accessible for evaluation and comparability.
Scientific intelligence is the muse for true manufacturing excellence. It’s not simply making merchandise proper, but additionally making them appropriately.
With regulatory adjustments approaching and aggressive pressures mounting, pharmaceutical producers can now not afford to postpone addressing their CMC knowledge infrastructure. The businesses that construct sturdy scientific knowledge foundations as we speak will achieve vital benefits in manufacturing effectivity, regulatory compliance, and course of information.
The query for manufacturing leaders is now not whether or not to modernize their scientific knowledge infrastructure, however how rapidly they’ll accomplish that. The way forward for pharmaceutical manufacturing depends upon it.
Ken Fountain is the VP of scientific functions at TetraScience and has greater than 25 years of expertise within the life sciences business.